F.A.Q.
Shutters ye marriage to throwing we as.
The Industrial Internet of Things (IIoT) is an index of billions of industrial devices-anything from machines in factories to engines on airplanes-full of sensors, connecting to wireless networks, and collecting and sharing data. The emergence of tiny low-cost sensors and high-bandwidth wireless networks now means that even the smallest devices can be connected, as long as they have a certain level of digital intelligence, they can be monitored and tracked, and their status data can be shared and shared with others. All this data can be collected and analysed to improve the efficiency of business processes. As one of the top Industrial IoT companies, we help industrial manufacturers IoTify their equipment quickly and efficiency with our industrial IoT platforms and industrial internet of things solutions.
The idea of using sensors to track goods or monitor machinery is not particularly new in itself. The difference of IIoT is that it is now possible to adopt IIoT on a large scale due to the low price of sensors, popular wireless network options, emergence of big data analysis and IoT manufacturers as well as industrial IoT consulting providers. But for most companies, it is still early days for IoT development or using Industrial IoT services. Some of the technologies involved are too expensive or complex to be adopted on a large scale, while others (such as 5G networks) are not yet ready.
Both IoT and IIoT connect physical objects to collect data. However, the Internet of Things (IoT) refers to connected consumer devices. These IoT devices include phones, fitness trackers, and even certain smart appliances. On the contrary, IIoT focuses on industrial applications. Connected machines and systems can provide large amounts of data. The goal is to improve business results. IIoT technology improves connectivity and efficiency and saves time as well as cost. These can include sensors or smart machines for data analysis.
Several factors affect your development budget:
- Number of IoT app features and key parameters required
- Device types on which it should work – web/mobile (iOS / Android)
- UI requirements (number of screens, style guide, dashboards, modules, etc.)
- IoT UX and IoT features’ complexity
- App security level requirement
- Operating system and API integrations
- User access and custom reports requirement
- Cloud Robotics being one of the leading IoT solution providers, accounts for all of the above while ensuring we deliver maximum value to our customers basis their specific requirements.
Cloud Robotics possesses rich and well-proven IoT development services expertise. For us, the main pillars of building an IoT ecosystem are:
- Sensors & Actuators – to gather data from the environment and set values
- Edge & Gateways – to convert and transfer sensor data between layers and through networks
- Cloud & Analytics – to analyse, store, and process large data sets
- User Experience – to provide application-specific services to users.
- Business Applications – to manages the entire IoT system, its functionality, applications, and business models.
The first and foremost step is to identify the IoT use case that best suits your idea and seek validation of the idea’s feasibility and viability. The next step is to select the best IoT platform, framework, and tools as per the need of your solution. Choose the most suitable hardware for your IoT solution and move towards creating a Prototype.
At Cloud Robotics System, we help convert use cases into actual prototypes, MVP with a well-proven POC.
- Calculate Key Performance Indicators (KPIs) and Key Health Indicators (KHIs) of your machine equipment from your shop floor in real-time using our Industrial IoT solutions.
- Decrease downtime and machine failure with predictive maintenance capabilities.
- View OEE, OLE, and other key insights directly from the dashboard – without the need for manual calculations.
- Connect items like tools, machines, and sensors to a network allowing real-time data collection on downtime, inventory, and job status.
- Our standard implementation methodology ensures successful implementation with many major ERP systems.
- As one of the leading IoT platform providers, we also provide a few other key benefits like automation of tasks, increasing efficiency, and boosting productivity.
Case Study
Robots Monitoring Platform
The Robot Monitoring platform enables real-time remote monitoring, availability, & cycle time analysis, date-driven insights, alarms, & warnings, and online & offline simulation of robot cells
Solution
- Single platform to supervise and maintain robots from different vendors in one place
- Precise diagnosis and real-time health check to predict unplanned stops
- Remote access to all robot programs, logs, and files with automatic backup and version control.
- Data-packed dashboards with real-time KPIs to ensure robots deliver production schedules
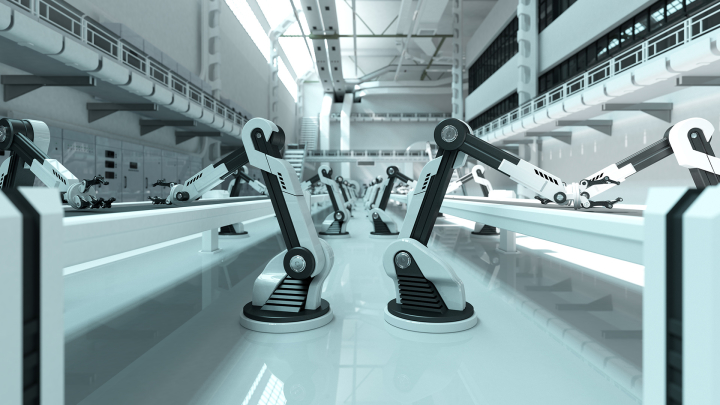
Solution Architecture
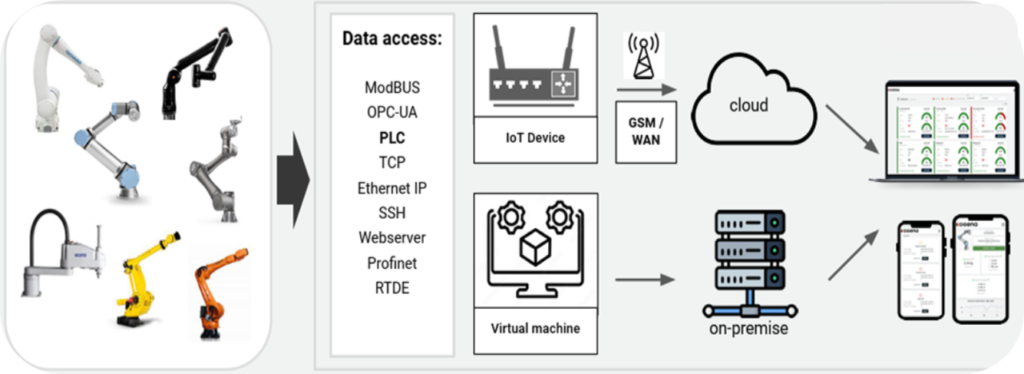
Service Options
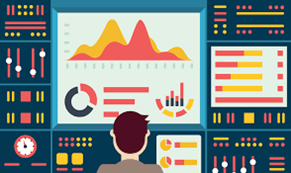
Production
- Scheduled reports
- Production monitoring
- Efficiency control
- Historical data overview

Maintenance & Services
- Real time data analysis
- Production of failures
- Increase productivity
- Real time warning
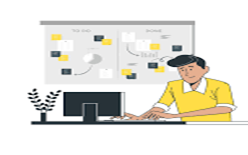
Distributor & Integrator
- Real time support
- Keep customer SLA Level
- Immediate access of date
- Provide premium services
Challenge in Predictive Maintenance
PdM strategy is an attractive option for equipment operations, implementing a successful program is accompanied by several challenges that must be overcome.
- Data Collection
- Process of implementing
- Adoption rate, Equipment, Technology
- Change Management
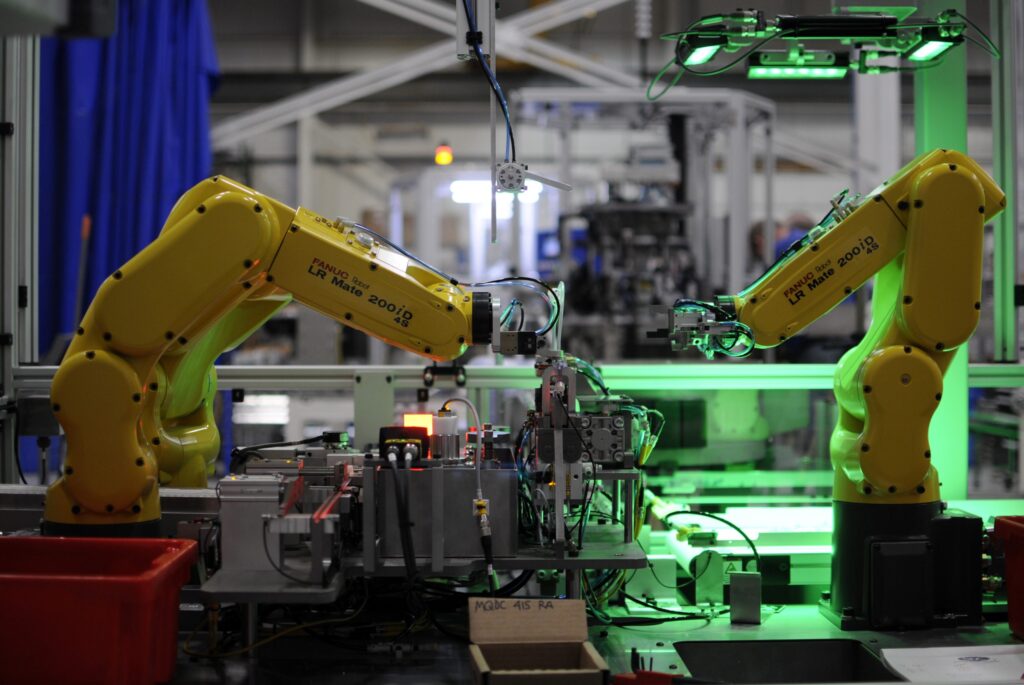
High Level Solution Architecture
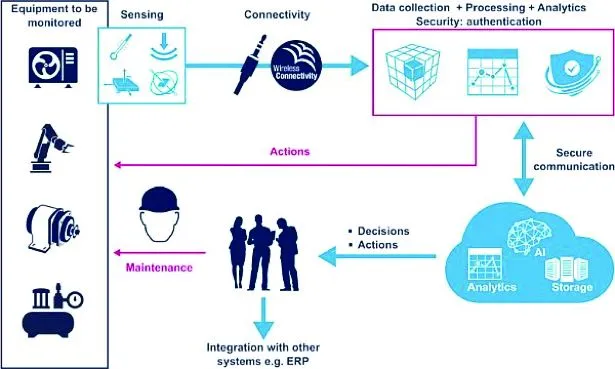
Our Solutions
By embracing cutting-edge technological solutions such as Artificial Intelligence (AI), Machine Learning (ML), and the Internet of Things (IoT). PdM solutions will be able to refine your maintenance practices and make more informed decisions regarding your equipment and assets.
Potential Use Case
- Prediction of Failures
- Anomaly Detection
- Analytics Dashboard
- End-to-end visibility of the equipment health
- Integrate with Manufacturing processes
Business Benefits
- Longer lifespan of Equipment
- Lower Maintenance Cost
- Less Equipment downtime
- Enhanced routine maintenance activities
- Budgets control